
- HIGH QUALITY IRON CASTING FOUNDRY FACTORY HOW TO
- HIGH QUALITY IRON CASTING FOUNDRY FACTORY PROFESSIONAL
Herein, this study focuses on the CO 2 emissions associated with cast iron production and introduces an interdisciplinary framework in order to study the environmental impact, technical performance and production costs. Therefore, there are evident knowledge gaps regarding the environmental impact of the foundry industry and the possibilities of decarbonizing the sector.

Although research activities have already given their attention to major industries such as steel, small sectors such as metal casting have been overlooked. The industrial sector is responsible for significant amounts of CO 2 emissions. In this present paper, an investigation is being carried out, along with some case studies, how the overall cost, including the energy-cost, in the Ductile Iron casting process could be reduced by implementing some good practices in foundry which includes proper methoding, modelling and simulation, optimization of facility layout, proper plant housekeeping, etc Importance of casting process simulation, which predicts the flow characteristics, is also discussed for reducing the energy and improvement of raw material efficiency of a foundry. Moreover, the formation of different casting defects is directly related to fluid flow phenomenon in the mold cavity during filling and the rate of cooling which affects the microstructure and the mechanical properties of the product. As the production of sound castings without any defect is always the main objective of a foundry, proper and intelligent methodings are suggested to improve the aesthetic look of the defect-free casting, which, in turn, will reduce fettling cost and rework. Improper gating design/ratio causes infilling, blow hole, shrinkage and cold shut defects. Method design is one of the critical areas which directly affect the casting quality. In the present scenario, where the selling price of products, especially Ductile Iron products, are not increasing so rapidly, the only way to cope up with the increasing energy and raw material cost is to reduce the production cost, which may involve proper and intelligent method design, implementation of software, and following some good practices in the foundry management. The cost of Energy, labour and raw materials increases day by day, which reduces the net profit margin of a Foundry. Over 50% of this energy is not utilized for the final casting itself, but is used for gating and risering systems. Physical laws determine an average energy input of 2,000 kWh per metric ton of final casting product. Melting and solidifying metals require a high amount of energy.
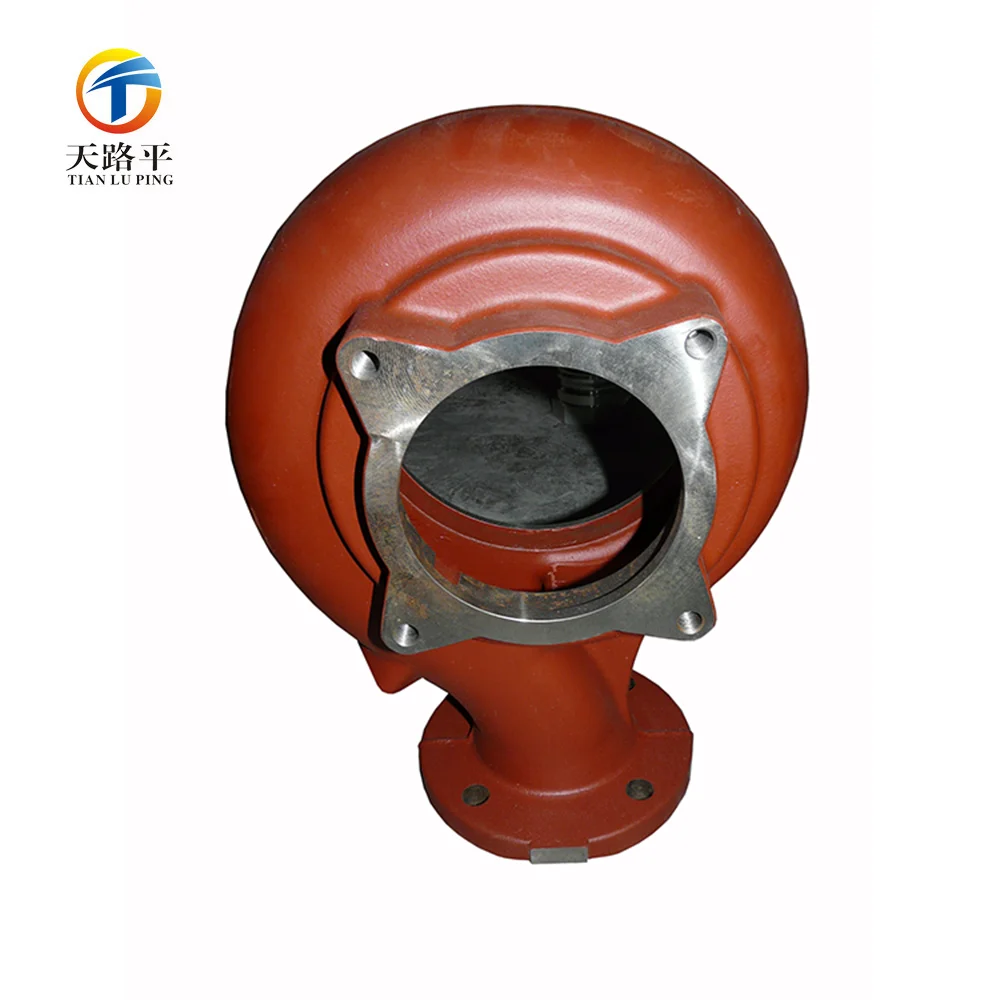
Thus Yide is always committed to providing high-quality but factory-price customized casting services for more and more customers in the whole world.The costs for energy and materials in foundries are 40% of the total cost.
HIGH QUALITY IRON CASTING FOUNDRY FACTORY PROFESSIONAL
As an established company with a long history and strong professional and technical strength, Jinma has enough ability to manufacture clay sand casting & precoated sand casting capacity over 20,000 tons, with the main products: Automobile Casting, Truck Casting, Cast Iron Fire Truck, Cast Iron Toy Tractors, Forklift Parts Casting/Hand Lift Casting, Agricultural Machinery Casting, Construction Industry Casting, Brass Casting, Bronze Casting, and Heat exchangers. is a newborn company from Ninghai Jinma (JM)Casting Foundry, founded in 1993. Meanwhile, we use inspection equipment to strictly monitor the grades of ductile iron castings.Thus can improve the properties of ductile iron castings, and strengthen the product’s tensile and impact resistance is greatly. In the production process of large-scale ductile castings, we generally use resin sand technology. When buying ductile cast iron parts, we cannot just look at the price, but also need to know about the product quality, service and casting technology. At the same time, we can also learn about the reputation of the foundry from the peers or the media. Generally, we can observe the manufacturer’s production ability and factory scale. First of all, we need to know the strength of the manufacturer. When choosing a casting foundry, we need to figure out the following points. Therefore, how can we choose a high-quality casting foundry? Of course, it is also important to choose a good ductile cast iron manufacturer. The reason why they are used is mainly because of their excellent properties.
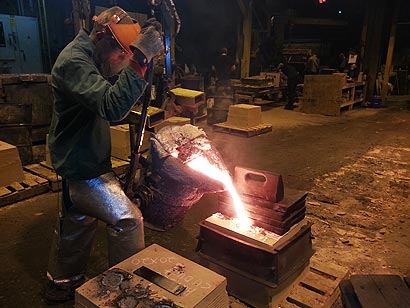
More and more ductile iron castings are used in all corners of national construction.
HIGH QUALITY IRON CASTING FOUNDRY FACTORY HOW TO
How to Choose a High-quality Casting Foundry
